The point of Enterprise Resource Planning software is to take full control of business operations. It’s a task a mature platform like MYOB Greentree is well up to – but, as anyone who works in the ERP field knows, no two businesses are the same. Not even two which operate in the same vertical. That’s why a level of customisation is inevitable in practically all software implementations. And that’s also why Verde Group has developed Verde extensions for MYOB Greentree.
These extensions provide the basis from which to customise multiple elements of the vanilla MYOB Greentree platform. The difference between using Verde extensions and a ‘tabula rasa’ customisation is that the former provides a defined, reusable framework in which most of the programming work is already done.
In simple terms, with Verde extensions, the necessary customisation to get your ERP system tailored to perfectly match those tricky business processes is faster, less risky and – crucially – has a minimal impact when it is time to upgrade your software to a more recent version (more on that in a moment).
Verde extensions are in use with more than 56 customers across a wide range of vertical industries. The extensions have a long history, developed over the course of nearly 15 years by a team of six developers led by Andrew Finn. The team writes, tests and supports the extensions, backed up by design contributions from an experienced and streetwise team which provides real-world business experience and advice. We’ve even got original Greentree product developers on the team.
We’ve opted to consolidate modifications into one of two schemas – Verde and VerdeSchema – instead of maintaining separate schemas for each client. This is a crucial element in the ‘repeatability’ of using the extensions as a flexible resource for the customisation of specific Greentree implementations.
With fewer sources of code, it is easier to overcome one of the major limitations to customisations, which we’ve already mentioned: upgrading and certifying your implementation when a new release of MYOB Greentree is available.
By using common schemas, we assess and prove the upgrade path internally which provides assurance and confidence for upgrade success on your site.
Commonality also means we can take customisations done for one customer and reuse the work for others, making the process of delivering a compromise-free solution that much faster and more cost-effective for everyone.
What we’ve learned from this approach is that the benefits tend to apply to customers operating in similar verticals. That was to be expected. Less expected are the occasions where a customisation for one industry is also very useful in another.
Let’s take a closer look at a specific example, the HAL extension designed to provide a just in time purchasing and fulfilment system.
The unusual business processes or situations where HAL can help include:
Just in time purchasing and fulfilment for branches. Highly configurable and employing complex forecast modelling, HAL automates turning backorders into Purchase Orders (PO), with Sales Order(SO)/PO linking. It provides PO ETA and status tracking, especially for long lead-time overseas orders. SO ETD updates and automatic notifications go to salespeople and customers when ETDs move outside a specified tolerance.
HAL handles automated stock reordering direct to POs and Location Transfer Requests (LTRs).
Automated Backorders to POs. When a new Backorder is created, Existing POs are searched. If a PO is found for the right supplier (Stock Item preferred supplier) that has undelivered and uncommitted stock (e.g. a stock order) then that stock is committed to the BO. If a PO is found that has not been sent to the Supplier (using the printed flag) then the requirement is added to the PO. If no PO is found then a new PO is created.
PO ETA and Status Tracking. HAL tracks back through all orders and deliveries by suppliers for the last 1-2 years and averages the number of working days from PO creation to delivery. When a PO is created, today's date is used for all ETAs by standard Greentree. Background processes run through the line items and if the line ETA date is the same as the PO creation date then the ETA is recalculated. This allows manual override by the user. Any date that is not the same as the PO create date is not touched.
SO ETD Tracking. Any SO on Backorder is notified to the Salesperson by email, or is available to them via WebView. When a Backorder's PO's ETA changes, the ETD on the SO is automatically updated. An audit trail of the ETD change is kept on Sticky Notes so the Salesperson can track what's going on. If appropriate, the customer can be emailed automatically with an ETD update.
Automated Stock Ordering. Using statistical forecasting techniques, HAL uses two steps – a daily calculation of the requirements for each Stock Item; 1) minimum stock is set at a level where there is a 95% chance that there will not be a stock-out. The maximum stock figure is not used in ordering, but is set to indicate the degree of variation found in historical sales. 2) With lead-times, expected forecast demand and a priority on preventing stock-outs (by Stock Item) a forecast purchasing requirement is determined and added to existing unsent POs or new POs are created using the same mechanism as used in the automated Backordering system. The process takes into account inter-branch transfers using the Location Transfer App in place of POs for branches to draw stock from a central warehouse.
Proof of the pudding
This functionality is implemented, up and running at RLB Packaging, a New Zealand company which runs multiple backorders as a standard business process. Finance and operations manager Steve Hazard explains why it chose HAL Extensions: “This is targeted at better managing stock quantity levels in the warehouse, with automated re-ordering and predictive management to reduce the working capital, space and other overheads associated with stock holding.”
Since implementing HAL extensions, Hazard says the main and most obvious benefit is a more visible, more automated supply chain, where purchasing specialists are alerted by the system to exceptions, rather than having to manually check and process back-orders. “If something is on a back-order, it has a window of an hour ahead of cut-off times for suppliers. As the sales orders get processed, the system automatically generates a purchase order and adds to it, before triggering that order within that window if the right volumes are reached to meet minimum order quantities for the particular supplier.”
Hazard adds that in simple terms, a lot of pernickety work which was previously manual is automated. “HAL encompasses and operates off a lot of complex business rules, which matches the nature of the products we supply. So, for example, if we have a product on which the lead time for delivery averages three days, it knows that and updates Greentree; when the PO is generated, it uses today’s date plus 3 days for expected delivery.
Read the full RLB Packaging case study here.
Requirements and future development
Verde maintains a single development environment which is always in step with the most recent certified Greentree version. This requires your implementation to also be on the most recent release.
It’s also important to note that we fully support the Verde extensions for our customers and other dealers through the Verde Help-Desk.
Customisation of ERP systems is an ongoing process and so too is the development of Verde extensions to cater for the ever-widening number of unusual business processes which must be addressed by MYOB Greentree.
We’re busy looking at how HAL can help cater for help solve the headache of end-of-month bubble sales, implement flexible stock-out levels and handle negative stock demand.
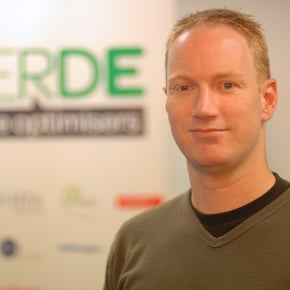