We might not have a single Walmart in New Zealand, but that doesn’t mean most of us don’t know what it is. There’s a reason this American behemoth of retail is world-famous: it puts products on shelves at ridiculously low prices. But how does Walmart do it? A good part of the answer lies in Supply Chain Optimisation.
It’s a similar story for other major retailers, including the big online ones like Amazon and AliExpress. By taking out absolutely every point of friction in the supply chain, these organisations can put products in the hands of consumers at properly attractive prices. And here’s the important lesson for any business: Supply Chain Optimisation isn’t just for the big boys. It’s something everyone should be doing.
In fact, some form or SCO is something that every business is doing to a lesser or greater extent, whether consciously or not (because you have to – managing your supply chain is fundamental to running your business). The real question, or issue, is whether or not you are doing it well or optimally. And let’s face it: who would want to do something called optimisation less than optimally.
There’s a good formal definition of SCO which belies the depth of the rabbit hole it truly represents: “SCO is the application of processes and tools to ensure the optimal operation of a manufacturing and distribution supply chain. This includes the optimal placement of inventory within the supply chain, minimising operating costs (which can include manufacturing, transport and distribution overheads. SCO often involves the application of mathematical modelling techniques using computer software.”
Yet, for most businesses, SCO happens as an organic process, evolving as your business grows. It’s a subset of Supply Chain Management – and that’s the broad range of activities required to plan your product's flow, from raw materials, to production and distribution, and on to the final customer. You will optimise where you notice the opportunities to do so – for example, by stockpiling if a raw material is intermittently available, by anticipating seasonal demand and ordering accordingly, and so on.
As an evolved process, many companies (perhaps yours included?) use the tools available on the day to get things sorted. That generally means bits of paper, or perhaps spreadsheets and word documents.
Nothing wrong with that, but there soon comes a point where your supply chain management starts falling down. It usually comes when business is good, too, because increased demand and bigger scale busts the seams of manual systems pretty darn quick.
And this is the point at which you need to consider better systems and along with better systems comes the potential for, you guessed it, the optimisation implied with SCO.
Here’s where the mathematical modelling techniques start becoming relevant. For most of us, the mere mention of that phrase is a little intimidating; maths is widely regarded as impenetrable.
And that’s why the ‘software’ part also becomes relevant. The beauty of maths (and by extension, when it is encoded in software) is that you don’t need to know the precise ‘how’ of it, so long as the outcome is trusted. Maths, for all its complexity, is also repetitive: do it once and every other time is precisely the same.
Here’s where the SCO component of a good ERP solution puts all that to your advantage. Forecasting tools help accurately anticipate demand using applying statistical trending. Unpredictability is factored in by setting safety stock levels, using statistical methods such as Standard Deviation and Mean Absolute Deviation. This feeds through to Production and distribution Planning. The level of detail possible is, frankly, remarkable: you can forecast down to individual customer demand. This leads to optimised inventory (model stock), which is then broken down into optimal stock units for transport and logistics purposes. Optimisation can even consider stackability constraints, load and unloading rules, palletising logic, warehouse efficiency and load stability. All that contributes to the most cost-efficient shipping.
This generally feeds into replenishment systems, with orders automatically generated to maintain the model stock.
Now that’s why we called it a rabbit hole: it can and does get very complex. But the advantage of having all that maths at your disposal in easy-to-use software, is perhaps obvious. It means the ability to cut costs out of the supply chain, and that’s always a good thing. More importantly, it means the ability to consistently meet demand for the products you supply.
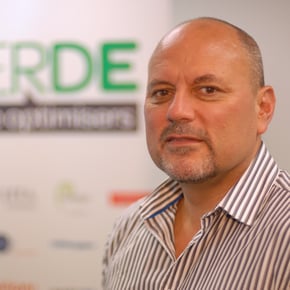